Tech
How does an Impeller Work?
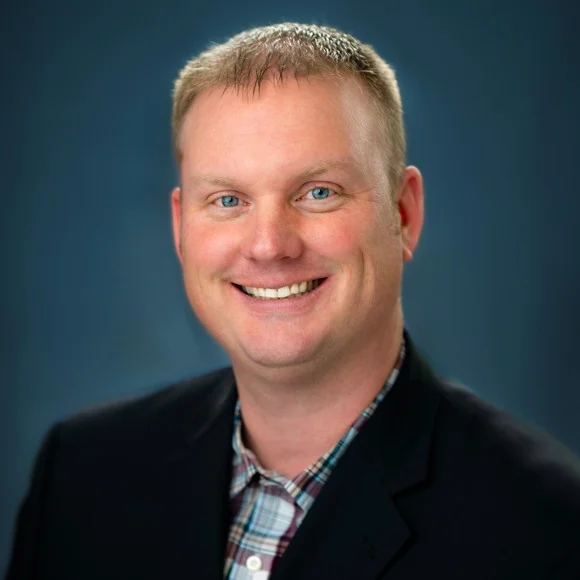
Published
1 year agoon
By
Jack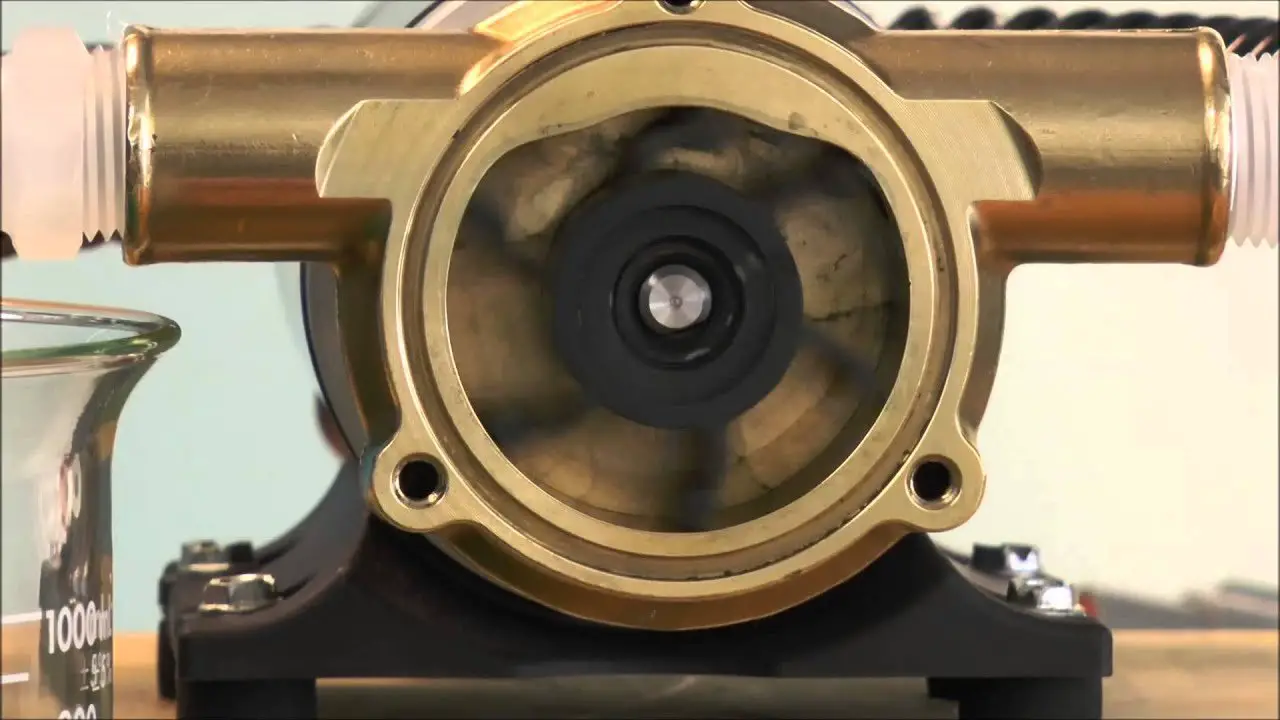
An impeller is a rotating part in the designing of a centrifugal pump that transfers energy from the pump motor to the fluid. These include blades that fall into the entrance to the central opening called the eye and create a centrifugal force as the liquid rotates from the chamber to the point of discharge.
There are different types of impellers, each with varying performance characteristics, so it is more or less used for specific applications than other impellers. Given its important role in centrifugal pump performance, it is possible to understand why impeller type and size are important in pump specifications.
Table of Contents
ToggleTypes of Impellers
The impellers have the following major types:
1. Open impellers
As the name suggests, the impeller blades are open on both sides without any protective cover.
Since they have no support on either side, they are weak, so they are generally used for smaller, cheaper pumps that don’t run under significant pressure. Although closed impellers can handle a certain level of solid content, they require more NPSH to operate without cavitation, damage, and loss of performance.
2. Semi-open impellers
The semi-open impeller has a rear wall cover which increases the mechanical strength of the blade by keeping it open on the other side. They lie between open and closed impellers in terms of efficiency and NPSH and are suitable for medium pumps with a small amount of soft solid. It should be noted that the distance between the half-open vanes and the pump cover must be small; otherwise, it will slip and overfill.
3. Closed impeller
Now that you know about open and half-open impellers, you can guess that closed impellers are closed in the front and back to provide maximum strength. They need less NPSH and provide better flow. However, they are more complex and expensive designs because they rely on long-distance wear rings to reduce axial loads and help maintain efficiency. They are the most popular impellers for large pumps that deliver clean liquids because they knock on contact with solids.
4. Vortex Impeller
Unlike the three impellers discussed above, the vortex impeller is not a channel impeller. In appearance, they are the same in the half-open type, but the scroll space is more significant, and the procedure is different.
Its design is suitable for dirty liquids containing waste and viscous solids. It creates a vortex/vacuum that removes solids from the impeller when the liquid is withdrawn, thus preventing damage inside. It has the least risk of clogging and has good solid mobility but is less efficient. Therefore, whirlpool importers should only be selected when necessary.
5. Cutter impeller
Like a vortex impeller, a shear impeller is designed to handle solids. However, they differ because they do not allow solids to pass through the vortices but instead have sharp blades designed to crush and remove the solids before they enter the pump. Although ineffective, they are ideal for impellers for pumping sewage and other waste because the fan duct may be blocked.
Effects of the Impeller diameter
When determining a centrifugal pump, in addition to the type of impeller, it is important to consider the diameter of the impeller because it will affect the pump performance.
The larger the impeller’s diameter, the greater the circular speed at the end of the impeller’s outlet, and therefore the greater the increase and current produced by the pump, and vice versa. In this case, the impeller can be cut to meet the specific duty point required by the program. The performance curve of most centrifugal pumps shows the size of the impeller setting range, making the pump run entirely. It is then used to determine the impeller diameter needed to meet performance requirements.
Changing the license is cheaper than using VFD to get the required points. However, the more the impeller is cut, the greater the distance between it and the body, resulting in a reduction in inefficiency. That is why there is a limit to the pump impellers that needs to be corrected.
Flow Characteristics
The impellers can be designed to share different flow characteristics in the pump or the center of the tank. Three different types of impellers flow designs can be used: axial, radial, and mixed.
Since centrifugal pumps are also classified in this way, the choice of impellers varies on the sample of pump characteristics and the flow characteristics of the impeller.
It moves the axial flow of the environment parallels to the impeller. It moves the radial current of the environment at right angles to the impeller itself.
The mixed flow impellers have the characteristics of axial flow and radial flow. They can move the environment at right angles at an angle other than the radial current.
Advantages and Disadvantages of the impeller
- Easy Maintenance
- Performance can be maintained by repeatedly adjusting the blades.
- The open design makes it easy to clean and remove the clogs. It is not necessary to disassemble the pump for adjustment or maintenance.
- The distance between the impeller and the body must be adjusted manually to compensate for the heat. This adjustment must be made at operating temperature, which can be dangerous.
- Use soft materials: Soft, non-sparking materials are required in some applications.
- Changing the blade (cutting and arching to increase capacity) is possible and inexpensive.
Author
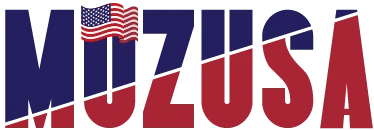